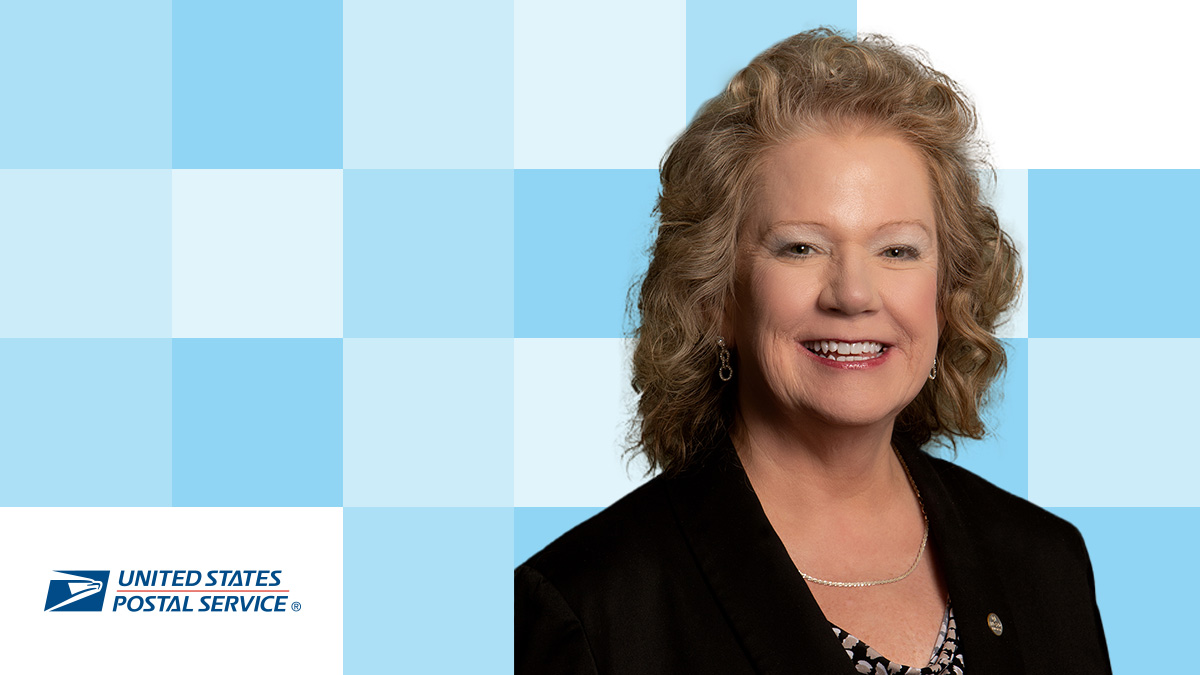
USPS Vice President Engineering, Linda Malone
Barely Touched by Human Hands
There are many ways we can point to the success of the Delivering for America® plan, but one of the clearest indicators is the dramatic improvement in our service performance. We can all understand this metric — if a letter or package arrives on time, things are working; if it’s late, there’s a problem. And thanks to the plan, we are showing our customers that things at USPS are working well, and a substantial part of the credit belongs to our enterprise-wide efforts to deploy the power of automation.
Things were very different before Delivering for America, or DFA. Years of financial hardship had made it impossible to adequately invest in our processing facilities. Many locations were neglected, and much of the equipment used to move mail and packages was poorly maintained, ill-suited for the drastic increase in package volume or simply too old to be useful. Too often, we had to resort to manual processing and daily workarounds just to keep our facilities moving, which regularly slowed processing — and our service performance — to a crawl. Something had to change.
Delivering for America was the change we needed. This plan recognizes that our revival can only be achieved if we give our employees the tools and strategies to succeed. At our processing facilities, this meant we needed to take away the heavy lifting and allow our employees to focus on managing the flow of our packages and mail.
My engineering systems team and I knew automation worked — USPS has been using it since the 1960s — but DFA brought a focus and commitment to automation, and parcel sorting equipment in particular, that we had never seen before at USPS. In the first two years of DFA, we made a bigger investment in automated technology than we had at any point in our history, and while it took a lot of hard work and dedication by my team, I’m proud to say we came through with flying colors. We doubled our daily package sorting capacity to 60 million — more than enough to handle any surge in demand.
The power of this decision was immediate, and this expanded processing capability has rewarded us with a boost in service performance that continues to grow to this day. Indeed, many of our key mailing categories are already at or close to the 95 percent on-time performance we’ve targeted for the end of DFA’s 10-year transformation.
And this is just the beginning. As we create a state-of-the-art, node-to-node processing network built around regional processing and distribution centers, local processing centers, and sorting and delivery centers, the power of automation will grow. Better, faster, bigger equipment laid out for optimal workflow will allow us to process volumes of mail and packages unimaginable only a few years ago. We’ll also be able to accept packages from business customers of all sizes, from the smallest sellers to the largest retailers, right at our facilities, offering unprecedented access to the world’s largest mailing and distribution network.
Automation makes this work. The fewer times we touch a letter or package, the faster we can process it. Modern automation can be 10 to 20 times faster than manual processing, and some of our newest machines can sort 6,500 packages and 17,000 letters, magazines and catalogs — what we call flats — every hour. This is a phenomenal capacity to have and will be a critical factor in making DFA’s vision a reality.
As technologies advance, so will the Postal Service’s investment in automation. We are already looking at robotic options to unload trucks and feed sorters, as well as new systems that essentially add automation to our existing automation. All of this will further enhance the speed and accuracy of our mail and package workflows and ensure we produce better on-time delivery performance for our customers — locally, regionally and nationally.
Automation also helps us create a better work environment. It allows our employees to be safer, more comfortable and more effective while optimizing our resources to their fullest. Automation is the tool that will enable us to reach the high service standards we know we can deliver and ensure we remain a world leader in our field and an essential part of every American’s daily life.
Linda Malone
Vice President, Engineering Systems